Рис. 5. Дистилляционная установка
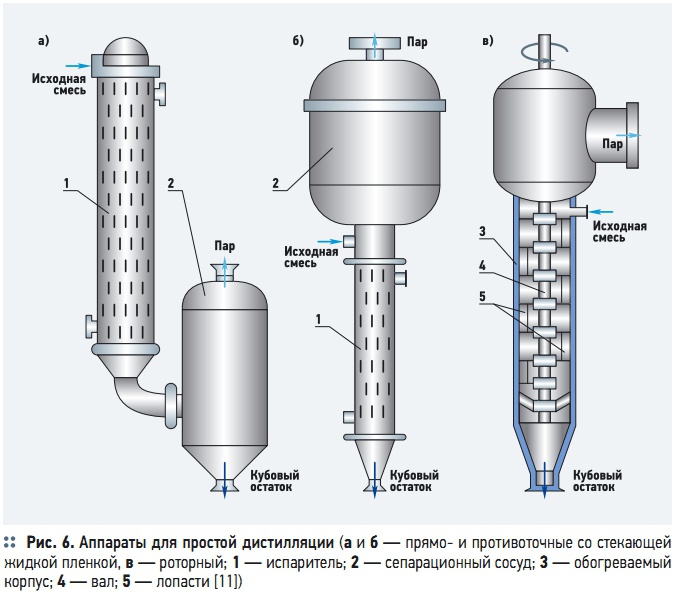
Рис. 6. Аппараты для простой дистилляции
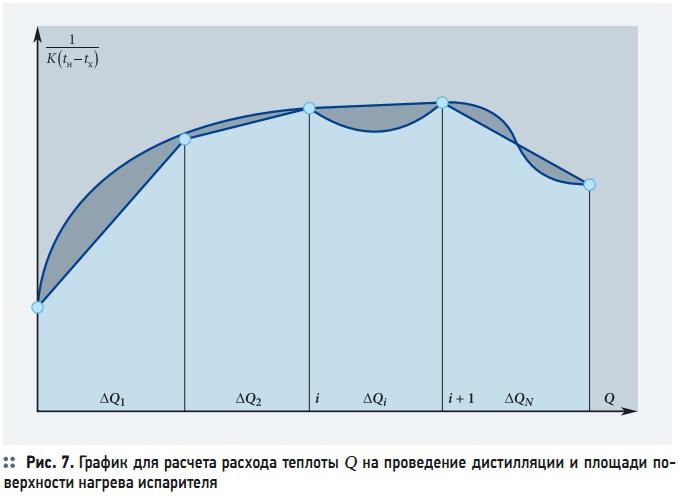
Рис. 7. График для расчета расхода теплоты Q на проведение дистилляции и площади поверхности нагрева испарителя
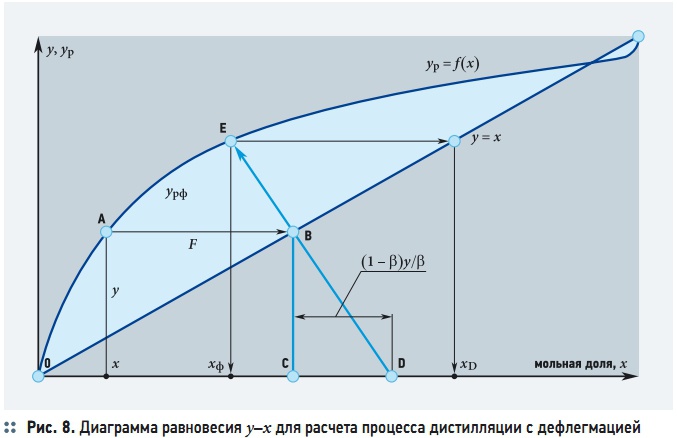
Рис. 8. Диаграмма равновесия у–х для расчета процесса дистилляции с дефлегмацией
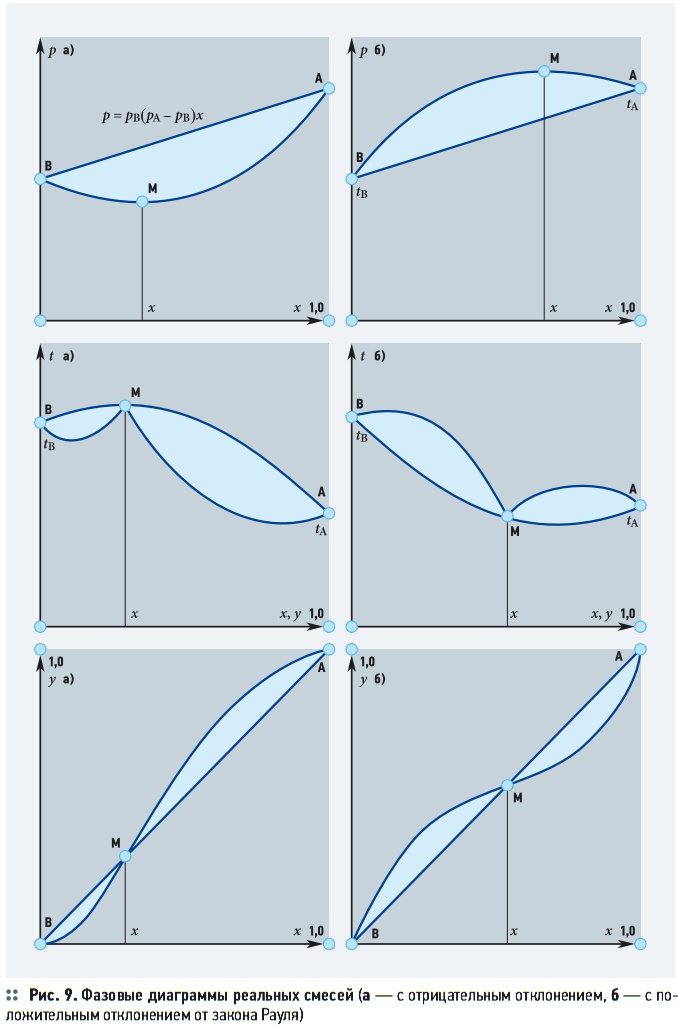
Рис. 9. Фазовые диаграммы реальных смесей
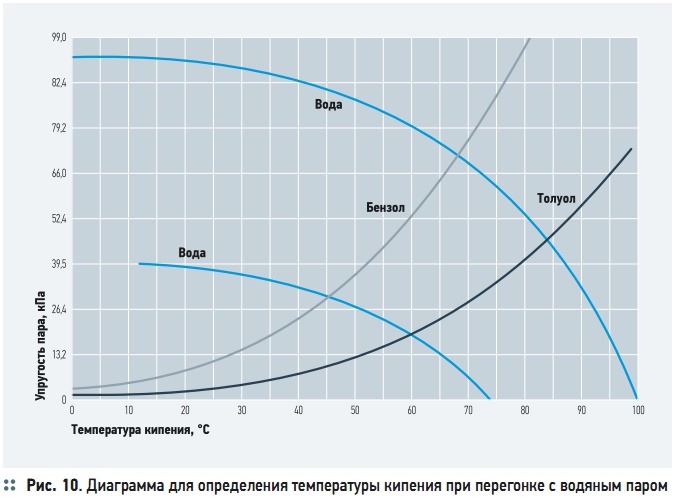
Рис. 10. Диаграмма для определения температуры кипения при перегонке с водяным паром
Классификация и расчет дистилляционных аппаратов
Аппараты, применяемые для дистилляции, подразделяются на емкостные и пленочные [9]. В емкостных аппаратах обрабатывается большой объем жидкой смеси, интенсивно перемешиваемой в результате кипения. Состав образующегося пара близок к равновесному и определяется по уравнению:
где n — число компонентов в водной смеси; хi и xk — содержания компонента i и k в жидкости. Типовая дистилляционная установка состоит из испарителя 1, снабженного теплообменным устройством для подвода к воде нужного количества теплоты; дефлегматора 2 для частичной конденсации пара, выходящего из испарителя (при фракционной дистилляции); конденсатора 3 для конденсации отбираемого пара; холодильника 4; сборников дистиллята 5 и кубового остатка 6 (рис. 5).
Для повышения эффективности разделения дистилляционные аппараты могут снабжаться двумя или более конденсаторами, работающими при различных температурах, что дает возможность разделять смесь на несколько фракций. Применяют также многоступенчатые противоточные аппараты, коэффициент разделения смеси в которых во много раз больше, чем в одноступенчатых [10]. Дистилляционные аппараты используют как для периодической, так и для непрерывной дистилляции [11].
В первом случае содержание низкокипящих компонентов в паре постепенно убывает, и средний состав дистиллята является промежуточным между составом паров, находящихся в равновесии с жидкой смесью, и кубовым остатком. Во втором случае состав жидкой смеси в аппарате практически идентичен составу кубового остатка, а состав дистиллята — составу равновесного с этой жидкостью пара.
Поскольку дистиллят образуется в результате парообразования смеси конечного состава с наименьшим содержанием низкокипящих компонентов, в емкостных аппаратах при непрерывной дистилляции достигается меньшая степень разделения жидкой смеси, чем при периодической дистилляции. При расчете дистилляции n-компонентной смеси обычно задано распределение одного или нескольких целевых компонентов между дистиллятом и кубовым остатком или относительное количество отгоняемого дистиллята.
В общем случае имеется 2n – 1 неизвестных: n – 1 значений хiд, n – 1 значений xiк и Wк или Wд. Для их определения при расчете периодической дистилляция существует n уравнений материального баланса (для всего процесса в целом и для n – 1 отдельных компонентов) и n – 1 уравнений, которые решаются совместно с n – 1 уравнениями фазового равновесия (24). В этих расчетах необходимо решить систему 2n – 1 уравнений, из которых n уравнений — алгебраические, а n – 1 — интегральные.
Аналитическое решение такой задачи чрезвычайно сложно, поэтому расчеты выполняются численными методами. При этом задают относительное содержанием всех компонентов в одном из продуктов разделения (дистилляте или кубовом остатке). Наиболее простой метод — поинтервальный, который заключается в совместном решении уравнений, описывающих условия фазового равновесия, и уравнений материального баланса (9) и (12), записанных в конечных разностях.
Для одного интервала ΔW/W принимается определенное значение относительного изменения количества дистиллируемой жидкости и последовательно вычисляется изменение ее состава, то есть для каждого интервала находится изменение содержания всех имеющихся компонентов Δxi. В первом приближении состав пара уi рассчитывается по уравнениям (24) как равновесный с жидкостью, состав которой соответствует началу интервала.
Расчет заканчивается при достижении заданного распределения целевых компонентов между дистиллятом и кубовым остатком. Состав дистиллята находится усреднением составов пара, получающегося во всех последовательных интервалах. Критерий правильности расчета — совпадение этого среднего состава дистиллята с найденным по уравнениям материального баланса. При непрерывной дистилляция n-компонентной смеси состав дистиллята, совпадающий с составом пара, образующегося при кипении кубовой жидкости (хiд = уi), вычисляется по (21), в которой хi и xk — содержания компонентов i и k в кубовом остатке. Имеем систему 2n – 1 алгебраических уравнений, связывающих 2n величин: Wд, Wк, n – 1 значений хiд и n – 1 значений хiк.
Для решения этой системы уравнений достаточно задать любую из перечисленных величин. Ввиду нелинейности уравнений (21) аналитическое решение практически невозможно и приходится использовать численные методы. Дистилляцию многокомпонентных смесей рассчитывают с применением современных методов ЭВМ. В пленочных аппаратах кипящая жидкость распределяется по поверхности нагрева в виде пленки.
По способу ее образования различают: аппараты с жидкостью, свободно стекающей по обогреваемой поверхности, например, по поверхности труб с помощью специальных распределительных устройств (рис. 6а–б), а также с восходящим движением жидкости за счет силы трения на границе между водой и паром, движущимся снизу вверх с достаточно большой скоростью; роторные — с водой, растекающейся по внутренней поверхности обогреваемого корпуса при вращении ротора с неподвижными или подвижными лопастями (рис. 6в).
По характеру движения фаз пленочные аппараты подразделяются на прямои противоточные. Объем и время пребывания жидкостей в пленочных аппаратах очень малы, поэтому они используются только при непрерывной дистилляции и особенно эффективны при перегонке термолабильных компонентов и вязких растворов. Состав жидкости в пленочных аппаратах изменяется по высоте, что обусловливает изменение температуры и состава пара.
Жидкость и пар, между которыми происходит теплои массообмен, проходят через произвольное сечение аппарата и не находятся в равновесии. Скорость и влияние теплои массообмена на эффективность процесса определяются скоростями и характером движения фаз. Уравнение материального баланса для элемента высоты аппарата dh в этом случае имеет вид:
d(Gyi) = –d(Wxi) = = –yipdG + Koy a(yi – yip)dh, (25)
где G и W — расходы пара и жидкости; yip — содержание компонента i в паре, находящемся в равновесии с жидкостью состава xi ; уi — состав пара, проходящего через сечение аппарата; Коу — коэффициент массопередачи; а — площадь поверхности массообмена на единицу высоты аппарата. При отводе образующегося пара (теплои массообмен с жидкостью исключены) уравнение (25) преобразуется в уравнение простой дистилляции.
Поскольку Коу > 0, знак второго слагаемого в правой части этого уравнения зависит от характера движения фаз. Вследствие преимущественного превращения в пар относительно более летучих компонентов содержание их в жидкости постепенно снижается, и она обогащается относительно менее летучими компонентами. Соответственно уменьшается содержание низкокипящих компонентов в равновесном паре.
Поэтому при одинаковом направлении движения жидкости и пара последний поступает в произвольное по высоте сечение аппарата с содержанием низкокипящих компонентов уi, превышающим их содержание уip в паре, равновесном с жидкостью, которая проходит через то же сечение. Из-за градиента концентраций уi – уip возникают поток относительно более летучих компонентов из пара в жидкость и встречный поток относительно менее летучих компонентов из жидкости в пар.
При большой скорости массообмена состав пара на выходе из аппарата приближается к равновесному с жидкостью конечного состава. При встречном движении фаз через произвольное сечение аппарата проходит пар с меньшим содержанием низкокипящих компонентов, чем отвечающее равновесию с жидкостью в этом сечении аппарата.
Поэтому благодаря массообмену из жидкости в пар переходят главным образом низкокипящие, а в противоположном направлении — высококипящие компоненты. В результате на выходе из аппарата пар по составу приближается к равновесному с исходной смесью, имеющей наибольшее содержание низкокипящих компонентов, то есть достигается дополнительное по сравнению с простой дистилляцией разделение смеси.
Расход теплоты Q на проведение дистилляции определяется по уравнению теплового баланса. Если в аппарат первоначально загружено W1 [кмоль] жидкой бинарной смеси с концентрацией низколетучего компонента х1, непрерывно подводится W1 [кмоль/с] той же смеси, а отводится W2 [кмоль/с] паров дистиллята (непрерывный процесс), уравнение теплового баланса принимает вид:
Q + (W1 + W1 ?r)ix ? = W2ix ? + (W1 + W1r – W2)iд, (26)
где W1 — количество исходной бинарной смеси, кмоль; х1 — концентрация низкокипящего компонента в смеси, кмоль; W2 — количество паров дистиллята, кмоль; ix ? и ix ? — энтальпии исходной жидкой смеси и кубового остатка; iд — энтальпия паров дистиллята. В случае W1 ? = 0 (периодический процесс) получим:
Q + W1ix ? = W2ix ? + (W1 – W2)iд. (27)
Площадь поверхности нагрева испарителя находится из уравнения теплопередачи с учетом изменения коэффициента теплопередачи и разности температур теплоносителя и кипящей жидкости с изменением ее состава во времени (при периодической дистилляции) или по высоте (при непрерывной дистилляции) [12].
При определении величины поверхности нагрева аппарата дистилляции периодического действия F следует учитывать, что процесс протекает в условиях нестационарного конвективного теплообмена, то есть при непрерывном росте температуры кипения жидкости tx и падении коэффициента теплопередачи К. Если перегонный куб обогревается конденсирующимся паром с температурой насыщения tнас, то поверхность нагрева F и продолжительность процесса τ связаны дифференциальным уравнением:
dQ = KF(tнас – tx)dτ, откуда (28)
Поскольку зависимости К и tx от Q сложны, то расчет по уравнению (29) проводится графически, используя график, показанный на рис. 7.
ΔQ1 = ΔQ2 = … = ΔQ4 = … = ΔQN, (30) где N — число точек разбиения.
Площадь трапеции:
откуда поверхность нагрева испарителя:
При дистилляции с дефлегмацией (конденсация преимущественно высококипящих компонентов при охлаждении смесей с целью их обогащения низкокипящими компонентами) зависимость состава пара уi , поступающего из испарителя в дефлегматор, с составами возвращаемой жидкости (флегмы) xiф и пара уiф, направляемого в конденсатор, определяется конструкцией и режимом работы дефлегматора. Обычно принимают, что выходящие из него жидкость и пар находятся в равновесном состоянии.
Тогда взаимосвязь xiф и уiф описывается уравнением (24), а количества и состава жидкости в аппарате — уравнением (13), в которое вместо уp подставляют уiф. Большая, чем при простой дистилляции, степень разделения смеси достигается благодаря частичной конденсации пара, образующегося в испарителе, и соответствующего увеличения расхода теплоты.
Расчет ведется графоаналитическим способом по диаграмме равновесия у–х для расчета процесса дистилляции с дефлегмацией (рис. 8). Для отгонки из смесей высококипящих компонентов с целью понижения температуры используют дистилляцию с водяным паром или инертным газом. Процесс основан на законе Рауля, справедливого для идеальных смесей вида «жидкость–пар» (рис. 8), согласно которому давление компонента в паре пропорционально мольной доле компонента в жидкости.
При постоянной температуре парциальное давление компонентов и общее давление паров над жидкой смесью P равно сумме парциальных давлений и находятся в линейной зависимости от мольной доли х легколетучего компонента. Если отгоняемое вещество А не смешивается с водой, то P = Pа0 + Pв (где Pа0 — давление пара чистого вещества А при температуре процесса; Pв — давление водяного пара), то есть общее давление является линейной функцией Pв, и вещество А можно отгонять при любой температуре, варьируя расход водяного пара или инертного газа Gуд.
Последний определяется соотношением:
где Mв и Mа — молекулярная масса воды (инертного газа) и отгоняемого вещества; η < 1 — степень насыщения водяного пара или инертного газа парами отгоняемого вещества по сравнению с равновесной степенью насыщения. Изменение парциальных давлений в зависимости от концентрации также изображают выпуклыми или вогнутыми кривыми (рис. 9). Диаграммы фазовых равновесий для реальных растворов строят на основании экспериментальных данных.
Количественные отклонения от закона Рауля могут быть так велики, что ряд смесей при определенных концентрациях имеет постоянную температуру кипения. При этой температуре согласно закону Коновалова состав равновесного пара над жидкой смесью равен составу жидкой смеси, то есть ур = х (точка М на рис. 9). Такие смеси обозначаются азеотропными и могут быть с максимальной или минимальной температурой кипения по сравнению с жидкой смесью других составов.
При дистилляции в потоке водяного пара образуется паровая смесь, которая затем конденсируется и охлаждается. Конденсат разделяется в сепараторе на отогнанный компонент и воду. Перегонку с водяным паром проводят с целью понижения температуры кипения исходной жидкой смеси компонентов, кипящих при температурах свыше 100 °C, компоненты которой нерастворимы в воде.
При такой перегонке отгоняемый компонент получается обычно в виде смеси с водой при температуре кипения или атмосферном давлении — меньшем, чем температура кипения воды. Исходная жидкая смесь загружается в перегонный куб, в рубашку которого подается глухой насыщенный водяной пар. Внутрь куба в исходную смесь барботируется острый водяной пар. Пары, образующиеся при кипении смеси, поступают в конденсатор и далее в сепаратор, где конденсат разделяется.
Из сепаратора удаляются вода и нерастворяющийся в воде легколетучий компонент, который собирается в сборнике. Диаграмма для определения температур кипения при перегонке с водяным паром, которая определяется как точки пересечения кривой упругости водяного пара с кривыми упругости различных не смешивающихся с водой жидкостей, показана на рис. 10. По диаграмме температура перегонки бензола с водяным паром при атмосферном давлении составляет 69,5 °C, а при p = 0,0395 МПа — около 46 °C, толуола при атмосферном давлении — 85 °C. Отношение количества отогнанного компонента к количеству водяного пара
где Gк и Gв — массовые количества компонента и воды; Рк и Рв — давления паров отогнанного компонента и воды; Мк и Мв — молекулярные массы компонента и воды, соответственно. Парциальное давление водяного пара составит:
рв = Р – ?рк, (36)
где Р — общее давление; ? — степень насыщения. Тогда из формулы (31) получаем следующее:
Целевой компонент выделяется из конденсата тем легче и полнее, чем меньше его растворимость в воде. Если она значительна, необходимо отогнанный из воды целевой компонент подвергать сушке. Этого удается избежать при использовании инертного газа. Однако при этом усложняется выделение отгоняемого компонента из образующейся парогазовой смеси вследствие необходимости охлаждения ее до низкой температуры, а нагревание и охлаждение газа требуют применения теплообменных аппаратов с большой площадью поверхности из-за низкого коэффициента теплоотдачи от стенки к газу и от газа к стенке.
Поэтому данный метод применяется, когда дистилляция под вакуумом затруднительна или невозможна и проводится в емкостных аппаратах, снабженных барботажными устройствами для равномерного распределения пара или газа по всему объему жидкости.
Выводы
Дистилляционные установки применяются в зависимости от требуемых параметров: расхода и состава жидкой смеси; количества и состава дистиллята и кубового остатка; условий, определяющих требуемый коэффициент разделения смеси. Неизвестные параметры рассчитывают совместным решением уравнений материального баланса с учетом зависимости между составами контактируемых жидкости и пара.
Эта зависимость определяется физико-химическими свойствами жидких смесей, способами (простая или фракционная перегонка, ректификация, молекулярная дистилляция) и условиями (периодический, непрерывный процесс) процесса дистилляции, а также его аппаратурным оформлением. Следует отметить, что затраты при осуществлении процессов дистилляции связаны с большими затратами тепловой энергии, составляющими 40 % от стоимости разделяемого продукта (если проводить дистилляцию в вакууме, температура кипения понижается и дистилляция требует меньших тепловых затрат).
В качестве источников тепловой энергии (особенно при дистилляции воды) могут быть использованы атомные и тепловые электростанции.