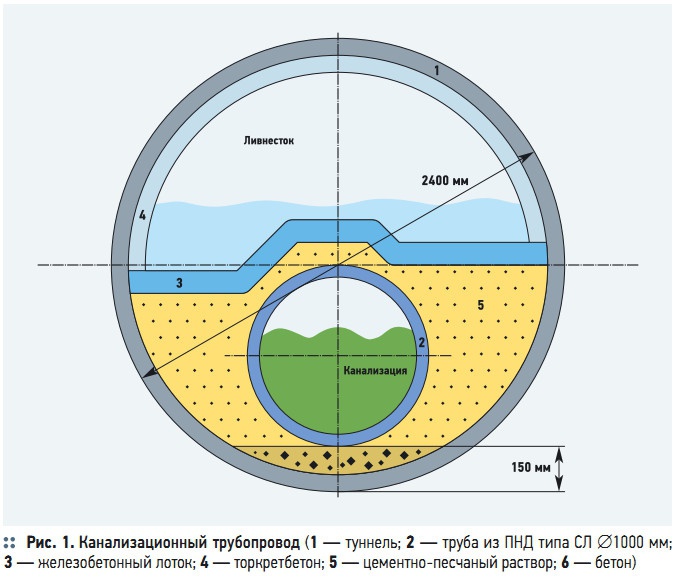
Рис. 1

Рис. 2
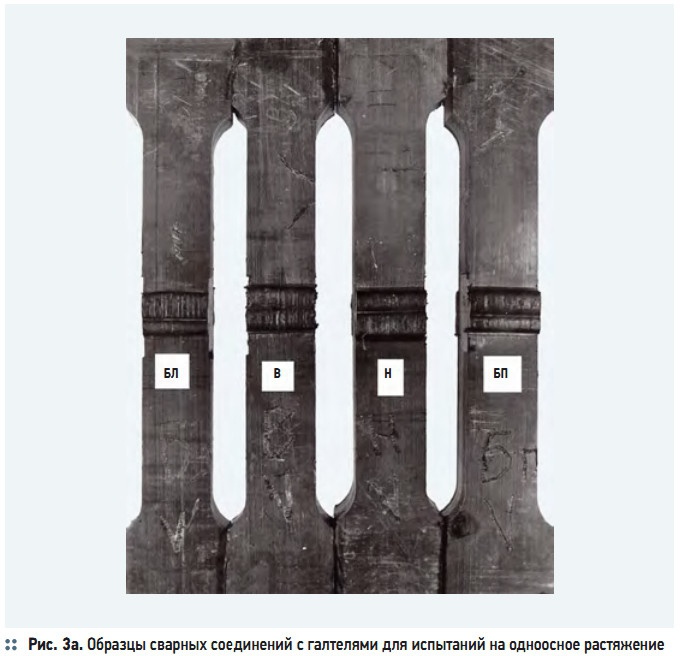
Рис. 3а
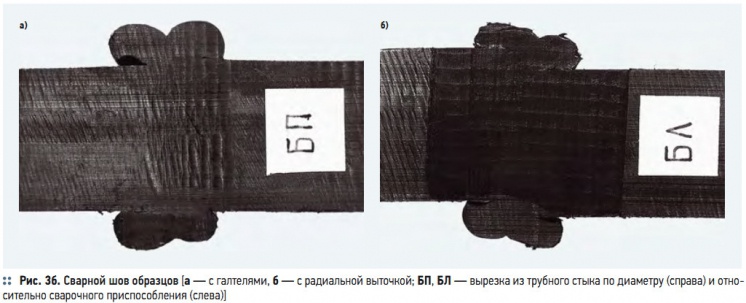
Рис. 3б
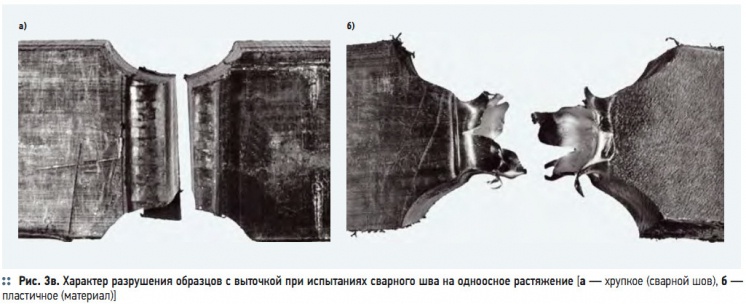
Рис. 3в
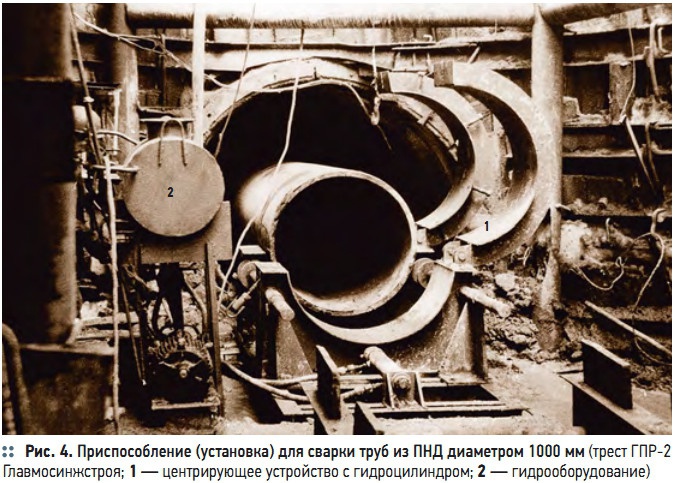
Рис. 4
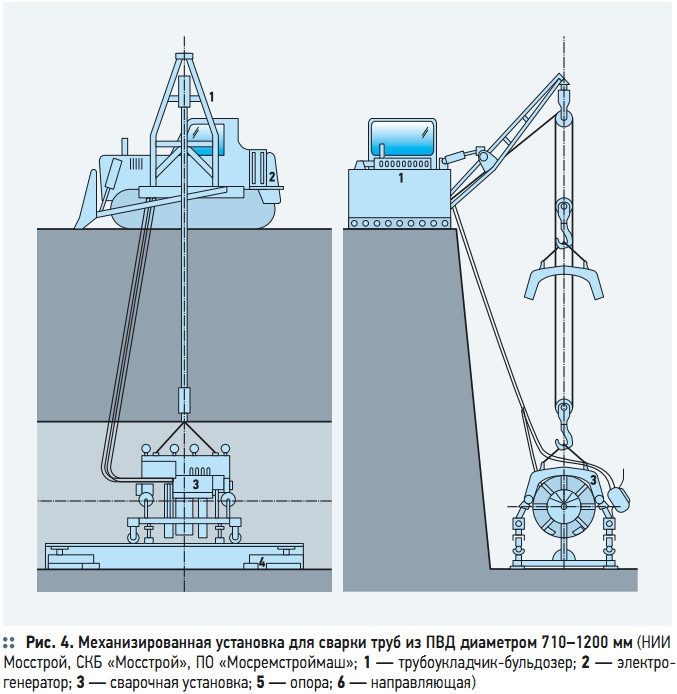
Рис. 5
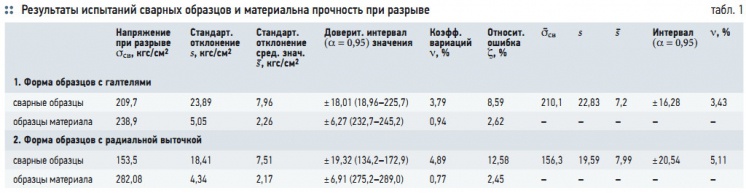
Табл. 1
Результатом этого явились: создание сооружения (в 1982 году), по которому сбрасываются канализационные стоки (по канализационному трубопроводу) и дождевые и талые воды — по верхней части коллектора; разработка (1982 году) и изготовление (1984 году) механизированной установки для сварки труб из ПНД диаметром 710–1200 мм и Дополнения к СН 478–80 (1983 году), в котором приведены нормы для качественного и производительного производства работ. Впервые в московской практике в 1982 году для строительства канализационного трубопровода (по адресу: Лианозово, микрорайоны 1 и 2) была использована промышленная партия труб из ПНД диаметром 1000 мм типа СЛ, изготовленная Казанским ПО «Оргсинтез» в III-м квартале 1981 года по Техническим Условиям (ТУ) 6-19-051-259–80.
Проект трубопровода разработан институтом Мосинжпроект ГлавАПУ города Москвы (проект №48112/с). В процессе проектирования во внимание принимались Рекомендации НИИ Мосстроя [1]. Данным разработанным проектом предусматривалось сооружение канализационного трубопровода, проходящего внутри тоннеля диаметром 2 м по его дну (рис. 1), из соединяемых между собой труб ПНД на сварке встык.
В этой связи, с целью обеспечения качественных сварных соединений труб из ПНД диаметром 1000 мм, в НИИ Мосстроя были проведены специальные исследования.
Трубопровод из ПНД заделывается в тоннеле (до шелыги) цементно-песчаным раствором. Над трубопроводом из ПНД устраивается железобетонный лоток и верхняя часть тоннеля используется как водосток. Общая протяженность коллектора 1400 м, глубина заложения (верх тоннеля) до 10 м. На трассе предусмотрено 17 смотровых камер и колодцев. Проект производства работ разрабатывался трестом «Мосоргинжстрой» Главмосинжстроя. Строительство коллектора производилось трестом Горнопроходческих работ №2 (ГПР-2) Главмосинжстроя. Им же производилась сварка и монтаж канализационного трубопровода из труб из ПНД при научно-техническом сопровождении НИИ Мосстроя.
Трубы из ПНД длиной 11,5 м доставлялись на строительный объект с базы Управления комплектации Главмосинжстроя автотранспортом, снабженным автоприцепом. Транспортировка производилась при температуре от 0 до –20 °C. Складирование труб на рабочем объекте осуществлялось в один ряд на поверхности, разровненной бульдозером и очищенной от крупных камней и строительного мусора.
Трубы длиной 11,5 м (5,7 м) опускались в котлован (предусмотренный для установки камеры). На дне котлован устанавливали сварочное устройство, скомпонованное с приспособлением для проталкивания сваренных плетей труб ПНД в тоннель. Сварка труб выполнялась сварочными приспособлениями, разработанных трестом ГПР-2 при консультации НИИ Мосстроя.
Центровка труб в приспособлении, зажатие концов в хомутах приспособления производились вручную. Установка диска между торцами труб и его подъем производились тельфером. Сварка труб устройством выполнялась двумя рабочими. Перед проведением сварочно-монтажных работ в котловане на поверхности была проведена пробная сварка труб, отработан оптимальный для данной конструкции устройства технологический режим сварки и обучен рабочий персонал. Сварка производилась как при положительной температуре воздуха, так и при температуре –10 °C. Сварка труб в котловане производилась в плети длиной до 100 м (в отдельных случаях до 300 м).
По мере сварки трубные плети проталкивали через специальное сварочное приспособление с открытыми хомутами в имеющийся туннель.
Для проталкивания использовалась разработанная трестом ГПР-2 домкратная установка (рис. 2) с техническими характеристиками: габаритные размеры (д × ш × в) — 12500 × 1380 × 500 мм; тип насоса — Н401Е, тип распределителя — 64ЕГ74-24, количество гидроцилиндров — 1 шт., ход штока — 900 мм; рабочая жидкость — масло турбинное 22 (по ГОСТ 32–74).
С целью улучшения движения по дну тоннеля и предотвращения повреждения переднего торца трубы спереди трубная плеть оснащалась лыжей из стального листа. При проталкивании трубных плетей удавалось преодолевать искривления трассы до 20°, причем смятия труб и разрушения сварных стыков не наблюдалось.
После проталкивания трубных плетей производилось заполнение цементнопесчаным раствором пространства между ними и стенкой тоннеля. Для предотвращения всплытия трубы из ПНД фиксировались в тоннеле распорками. После замоноличивания над трубопроводом из ПНД монтировалась стальная арматура и производилось бетонирование лотка, по которому при эксплуатации тоннеля через его верхнюю часть сбрасывались дождевые и талые воды.
В 1982 году канализационный трубопровод из труб ПНД сдан в эксплуатацию 5-му району канализационной сети треста Москанализация. Накопленный в ходе строительства коллектора опыт сварки и монтажа труб из ПНД использован при разработке Дополнения к Инструкции СН 478–80 [2]. Приобретенный опыт сооружения канализационного коллектора из труб ПНД оценивается проектировщиками, строителями и эксплуатантами положительно.
Начиная с 1983 года применение труб из ПНД для подземных сетей трубопроводов водоснабжения и канализации в городе Москве было расширено. В этой связи, с целью обеспечения качественных соединений труб из ПНД диаметром 1000 мм, получаемых сваркой встык на специально изготовляемой установке, в НИИ Мосстрое были проведены специальные исследования. Они включали изучение тепловых процессов и отработку технологии сварки с одновременной оценкой прочности сварных образцов.
При изучении теплового процесса сварки труб из ПНД уделялось внимание процессам нагрева и оплавления их торцов, определявших тепловую картину сварки и охлаждения оплавленных торцов труб в период технологической паузы, а также условиям течения расплава при осадке торцов. Известно, что тепловые процессы контактной сварки полиэтиленовых труб можно описать при определенных допущениях различными физико-математическими моделями. Во многих работах приведены результаты исследования тепловых процессов сварки, предоставленных задачей по абляции материалов и задачей Стефана.
Тепловой процесс сварки был сведен к задаче Стефана при следующих допущениях: температура нагревательного элемента постоянна в процессе нагрева; нагрев торца трубы тепловым излучением не учитывается; расплавленный материал не удаляется из зоны плавления; перепад температур по толщине стенки не учитывается; противоположный источнику нагрева конец трубы теплоизолирован; теплообмен на внутренней стенке трубы не учитывается; коэффициенты теплоотдачи не зависят от температуры. Числовое моделирование на ЭВМ «Минск-22» процессов оплавления и охлаждения полиэтиленовых труб большого диаметра (710–1200 мм) при контактной сварке встык, с использованием положений задачи Стефана и с учетом зависящих от температуры теплофизических коэффициентов материала, убедило в следующем.
Влияние диаметра труб (в рассмотренном диапазоне 710–1200 мм) на результаты расчетов несущественно (до ≈ 1 %). Влияние толщин стенок труб рассмотренных типов Л, СЛ и С на результаты расчетов малозначительно (до ≈ 10 %). Зависимости глубины оплавления кромок труб и глубины проникновения теплового потока от времени описываются функцией степенного вида. Глубины оплавления кромок труб диаметром 1000 мм тип СЛ составляют: при времени нагрева 200 с — 2,14 мм (температура воздуха +20 °C); 2,0 мм (0 °C) и 1,84 мм (температура воздуха –20 °C), время оплавления при значении глубины оплавления — 3 мм соответственно составляет 356, 445 и 540 с. Глубина проникновения теплового потока, вызывающего повышение температуры стенки трубы из ПНД до 20–22 °C при времени оплавления 500 с, составляет 5,5 см (температура воздуха +20 °C); 24,9 мм (0 °C) и 1,6 мм (температура воздуха –20 °C) — на основании этого длину выступающих из зажимов концов свариваемых труб с целью надежного их зажатия рекомендуется принимать не меньше максимального значения 5,5 см. Время охлаждения поверхности оплавленного торца трубы, при котором обеспечиваются минимально необходимые реологические характеристики материала шва, к моменту осадки (технологическая пауза) в среднем составляет при времени оплавления 600 с: 15,5 с (температура воздуха +20 °C); 13,2 с (0 °C) и 11,3 с (температура воздуха –20 °C); минимальное значение ≈ 11 с — это необходимо принимать в расчет при проектировании конструкций сварочного оборудования.
Соответственно были выбраны основные технологические параметры сварки труб диаметром до 1000 мм, а именно: ориентировочное время оплавления торцов труб (в зависимости от глубины оплавления и температуры наружного воздуха), максимально допустимые значения технологической паузы (в зависимости от величины температуры наружного воздуха).
Оптимальная температура сварки толстостенных труб из ПВД большого диаметра составляет 196–200 °C. Значения давления осадки при сварке толстостенных труб большого диаметра, по результатам этой работы выбрано 2 кгс/см2, давление при оплавлении — 1 кгс/см2.
Отработка технологии пробной сварки труб из ПНД диаметром 1000 мм одновременно прочностными испытаниями сварных соединений. Сварка образцов производилась на приспособлении, разработанном и изготовленном трестом Горнопроходческих работ №2 Главмосинжстроя при консультации НИИ Мосстроя, с использованием подготовки торцов труб под сварку вручную электрорубанком. Условия свайки: сварка трубных образцов выполнялась на поверхности земли в тепляке, защищающем место сварки от действия атмосферных осадков и ветра, температура наружного воздуха в период сварки образцов составляла от 5 до 15 °C. Всего было сварено 10 трубных образцов, для испытаний было отобрано пять.
Подготовительные операции (центровка, торцовка) производились вручную. Торцовка концов труб, закрепленных в зажимах центрирующего устройства, выполнялась электрорубанком ИЭ5701АУ2. Зазоры по границе контакта, подготовленные к оплавлению торцов труб, достигали 3 мм, несовпадение кромок составляло максимально 5 мм (или 12 % от толщины стенки трубы).
При этом использовался следующий технологический режим сварки образцов: температура на рабочей поверхности нагревательного элемента (по показаниям прибора КВП1-503, скорректированным по показаниям потенциометру КСП-4), находилась в момент оплавления торцов труб в пределах от 190 до 240 °C; время оплавления составляло от 7 до 10 минут; технологическая пауза составляла от 8 до 20 с; давление при оплавлении колебалось в пределах от 0,96 до 1,2 кгс/см2 (тарировка по манометру насосной станции — от 16 до 20 ати) и поддерживалось в процессе оплавления; давление осадки колебалось в пределах 2,5– 3,68 кгс/см2 (по манометру — от 43 до 60 кгс/см2); время охлаждения стыка под давлением осадки около 40 минут. Из последних пяти сварных трубных образцов были вырезаны фрезерованием линейные образцы-лопатки: с галтелями (длина — 300 мм, длина и ширина зажимной части — 40 × 60 мм, радиус галтели — 60 мм) и с радиальной выточкой (300 × 60 мм, радиус выточки 50 мм).
Из каждого трубного образца были вырезаны по четыре образца указанных форм и размеров (расположение относительно центрирующего устройства установки — сверху, снизу и сбоку). Всего было подготовлено 20 образцов. Сварочные валики на образцах не удалялись. Для сравнительных испытаний из трубы были вырезаны 10 контрольных образцов аналогичной формы и размера.
На рис. 3а показаны подготовленные к испытаниям образцы с галтелями. На рис. 3б приведены макрофотографии сварного шва. На указанных фотографиях граница шва не просматривается. Испытания проводились на одноосное растяжение с учетом требований ГОСТ 11262–76, ТУ 6-19-051-259–80 (пункт 4.3), проекта стандарта СЭВ «Рекомендация по стандартизации. Сварка пластмасс. Испытание пластмассовых соединений на растяжение». Испытания проводились на универсальной разрывной машине типа УММ-50 при скорости растяжения 50 мм/мин. Напряжение при разрыве образцов, отобранных из верхней части сварного соединения относительно зажимных хомутов приспособления на 22–53 % ниже, чем образцов, отобранных из нижней части, что свидетельствует также о неравномерности оплавления торцов труб и приложения сварочных давлений.
Следует отметить незначительное различие в значениях σсв и σсв1 (в пределах до 1 %), следовательно, при вычислении разрушающего напряжения правомерно оперировать площадью рабочей части образца. Более значительным являются различия в результатах испытаний образцов двух форм — с галтелями и с радиальной выточкой: по прочности сварного шва в 1,36 раза, по прочности материала — в 1,18 раза. Разброс показателей при испытаниях образцов с выточкой выше по коэффициенту ν в ≈ 1,5 раза. Относительная деформация образцов при разрыве составляет 154,5 и 36,3 %. Следовательно, эффект концентрации, создаваемый выточкой необходимо учитывать при оценке истинного значения (разрушающего напряжения). Здесь отметим, что предел текучести материала, определенный по ГОСТ 11262–80, составляет 256 кгс/см2. Коэффициент формы, характеризующий влияние выточки в данном случае составит 0,73.
Результаты испытаний на прочность при растяжений (табл. 1) приведены с учетом определения разрушающего напряжения из расчета по площади рабочей части образцов σсв и по площади контакта торцов при сварке σсв1. Анализ результатов испытаний показывает следующее. Характер разрушения сварных образцов обеих форм, как правило, хрупкий. Рис. 3в иллюстрирует характер разрушения сварного шва и материала у образцов с выточкой.
При сварке труб диаметром 1000 мм на приспособлении с подготовкой кромок труб вручную при площади электрорубанка и установленном технологическом режиме прочность сварных стыков ниже прочности основного материала. Коэффициент качества сварки составляет 0,88 (доверительный интервал 0,716–0,946) при испытании образцов (с галтелями) и 0,54 (0,475–0,675) при испытании образцов (с выточкой), что объясняется несовершенством использованного сварочного оборудования. Это также подтверждается заметным разбросом прочности по периметру сварного соединения трубных образцов. Так, на основании результатов прочности испытаний можно сделать общий вывод о недостаточной прочности сварных соединений труб диаметром 1000 мм, полученных на сварочном приспособлении данной конструкции (без элементов автоматического регулирования технологического режима сварки), предусматривающей использование ручных процессов в ходе подготовки кромок и их сварки.
Было принято допущение о том, что для как самотечного канализационного трубопровода, проходящего в тоннеле и дополнительно забетонированного, полученная прочность сварных швов вполне достаточна. Это позволило произвести сварочно-монтажные работы с трубами из ПНД диаметром 1000 мм.
Разработка оборудования для сварки труб из ПНД
В 1981–1982 годах для сварки труб из ПНД диаметром 1000 мм трестом Горнопроходческих работ №2 (ГПР №2) Главмосинжстроя были разработаны рабочие чертежи СВП.00.00 на монтажное приспособление (установку). Два образца установки были изготовлены Механическим заводом Главмосинжстроя (нагревательные инструменты были изготовлены заводом по ремонту дорожных машин). В комплект установки входили: устройство для сварки с гидрооборудованием (рабочие чертежи №СВП-01), нагревательный элемент (рабочие чертежи №СВП-02), а также электрорубанок ИЭ5701А42 (по ГОСТ 8306–73) и ручная циркулярная электропила ИЭ510213 (по ГОСТ 11094–73).
Техническая характеристика устройства для сварки: диаметр свариваемых труб — 1000 мм; производительность — два стыка в смену; ход подвижного хомута — 850 мм; ход гидроцилиндра — 480 мм; габаритные размеры (д × ш × в) — 3000 × 1300 × 1550 м. Гидрооборудование: тип насоса — И-401Е; тип предохранительного клапана — 64НГ74-24; количество клапанов — 2 шт. Рабочее давление при оплавлении — 18 кгс/см2, при осадке — 43 кгс/см2. Основной технической характеристикой инструмента являлась мощность его электронагревателя. НИИ Мосстрой был произведен расчет мощности нагревательного инструмента. Тепловая мощность инструмента в общем виде определяется суммой расхода тепла на нагрев массы диска до рабочей температуры Qм, теплопотерями Qтп и расходом тепла на оплавление торцов труб Qпэ. При назначенных размерах нагревательного инструмента, имевшего кольцевую форму: наружный диаметр 1100 мм, внутренний — 820 мм, толщина 30 мм и масса (сталь) — 99 кгс.
При нагреве инструмента от температуры 20 °C до температуры 200 °C величины Qм и Qтп составили 5962 и 3634 ккал/ч, соответственно. Расход тепла на оплавление торцов труб из ПНД диаметром 1000 мм типа СЛ определяли как:
Qпэ = 2NF √τ = 800 ккал, (4.1)
где N — коэффициент, определяемый свойствами ПНД и температурой инструмента и окружающий среды, принято N = 3000; F — площадь оплавляемых торцов труб, подсчитано F = 0,063 м2; τ — время оплавления, принято τ = 3600 с. Расчетная мощность электронагревателя при этом составила 13,7 кВт. Рабочая температура нагревательного приспособления контролировалась прибором КВ1П-603 (ГОСТ 7164–76) с хромель-капелевой термопарой ХК.
На разработанном приспособлении производилась пробная сварка труб диаметром 1000 мм и отработка технологического режима сварки. После проведения приемочных испытаний первого образца приспособления (акт приемки Ведомственной комиссии Главмосинжстроя от 03.06.1982 г.).
Недостатками сварочного приспособления является низкая фактическая производительность (1,6 стыка в смену) и нестабильное поддержание технологических параметров сварки.
С учетом замечаний комиссии был изготовлен второй образец. Оба образца приспособления были использованы при сварке канализационного коллектора из труб ПНД диаметром 1000 мм в микрорайонах 1 и 2 Лианозово.
На рис. 4 показана сварочная установка и гидрооборудование, установленное в котловане. НИИ Мосстроем и СКБ «Мосстрой» в 1980–1981 годах разработана механизированная установка для сварки труб из ПНД в диапазоне диаметров от 710 до 1200 мм (рабочий проект СКБ «Мосстрой» №5622).
Установка состоит из собственно сварочной установки, переносных направляющих, располагаемых на опорах, базовой грузоподъемной и энергопитающей машины — трубоукладчика-бульдозера на базе трактора ДТ-75, оборудованного электрогенератором (рис. 5).
Техническая характеристика установки: диаметры свариваемых труб — 710, 800, 900, 1000 и 1200 мм; базовая машина — трубоукладчик-бульдозер на базе трактора ДТ-75; производительность — 10 стыков в смену; привод — гидравлический от гидросистемы трактора; давление в гидросистеме — 100 кгс/см2; привод механизма торцовки труб — от гидромотора типа МП-80/100; частота вращения дисков с резцами — 60 мин–1.
Максимальное время торцевания — 30 минут. Питание электронагревательных элементов напряжение от генератора — 36 В. Максимальная мощность — 0,8 кВт.
Максимальное время нагрева торцов труб до 210 °C — 20 минут. Максимальное усилие прижатия нагревательных элементов к торцам труб — 1250 кгс. Максимальное усилие сжатия труб — 3400 кгс. Скорость перемещения установки по направляющим — 0,05 м/с. Габаритные размеры (д × ш × в) — 1835 × 2260 × 1890 м. Масса собственно установки — 2600 кг. Масса с комплектными устройствами (без трубоукладчика) — 4500 кг.
Принципиальной отличительной особенностью конструкции сварочной установки является наличие и конструктивное устройство ее основного рабочего элемента совмещающей функции механизма торцовки труб и нагревательного инструмента. Указанное конструктивное отличие защищено авторским свидетельством СССР.
Другим конструктивным отличием установки является устройство гидравлической системы. В 1982 году производственное объединение «Мосремстроймаш» изготавливает опытный образец установки. Испытания и доводка установки проводились в 1983 году.
Заключение
Накопленный в ходе строительства коллектора опыт сварки и монтажа труб из ПНД большого диаметра использован при разработке Дополнения к Инструкции СН 478–80 [2], положения которой распространялись на трубы диаметром только до 630 мм. Здесь следует указать на то, что положения указанной Инструкции с Дополнением использовались в стране до 2000 года, пока не вышел в свет Свод Правил (СП) 40-102– 2000 [7]. (Дополнение к Заключению — Положения указанного СП позволяют вести строительство трубопроводов из полиэтиленовых труб большого диаметра и в настоящее время).
- Рекомендации о применению и сварке труб из ПНД диаметром до 1200 мм в строительстве подземных трубопроводов водоснабжения и канализации. НИИ Мосстрой. — М., 1982.
- СН 478–80.
- Сладков А.В. Расчет теплового процесса сварки полиэтиленовых труб // Сварочное производство, №1/1982.
- Голубева А.А., Соловьева Е.И. Сладков А.В. Исследование на ЭВМ теплового процесса контактной сварки полиэтиленовых труб большого диаметра. — Сб. науч. трудов НИИ Мосстроя, 1982.